Изборът на повърхностно обработка е проблем, с който се сблъсква всеки дизайнер. Налични са много видове възможности за обработка на повърхността и дизайнер на високо ниво трябва не само да обмисли икономиката и практичността на дизайна, но и да обръща внимание на процеса на сглобяване и дори екологичните изисквания. По -долу е кратко въведение към някои често използвани покрития за крепежни елементи въз основа на горните принципи, за справка от практикуващите закопчалки.
1. Електрогалванизиране
Цинкът е най -често използваното покритие за търговски крепежни елементи. Цената е сравнително евтина, а външният вид е добър. Общите цветове включват черно и военно зелено. Въпреки това, неговите антикорозионни характеристики са средни и неговите антикорозионни характеристики са най-ниските сред слоевете за цинк (покритие). Като цяло тестът за неутрален солен спрей на поцинкована стомана се провежда в рамките на 72 часа, а специалните уплътняващи агенти също се използват, за да се гарантира, че тестът за спрей за неутрален сол продължава повече от 200 часа. Цената обаче е скъпа, която е 5-8 пъти по-голяма от тази на обикновената поцинкована стомана.
Процесът на електрогалванизиране е предразположен към водородно премахване, така че болтовете над 10.9 обикновено не се третират с галванизиране. Въпреки че водородът може да бъде отстранен с помощта на фурна след покриване, пасивационният филм ще бъде повреден при температури над 60 ℃, така че трябва да се извърши отстраняване на водород след електроплаване и преди пасивация. Това има лоша операция и високи разходи за обработка. В действителност общите производствени предприятия не премахват активно водорода, освен ако не са упълномощени от конкретни клиенти.
Консистенцията между въртящия момент и силата на затягане на поцинкованите крепежни елементи е лоша и нестабилна и те обикновено не се използват за свързване на важни части. За да се подобри консистенцията на предварителното натоварване на въртящия момент, методът за смазване на покритие след покриване може да се използва и за подобряване и подобряване на консистенцията на предварителното зареждане на въртящия момент.
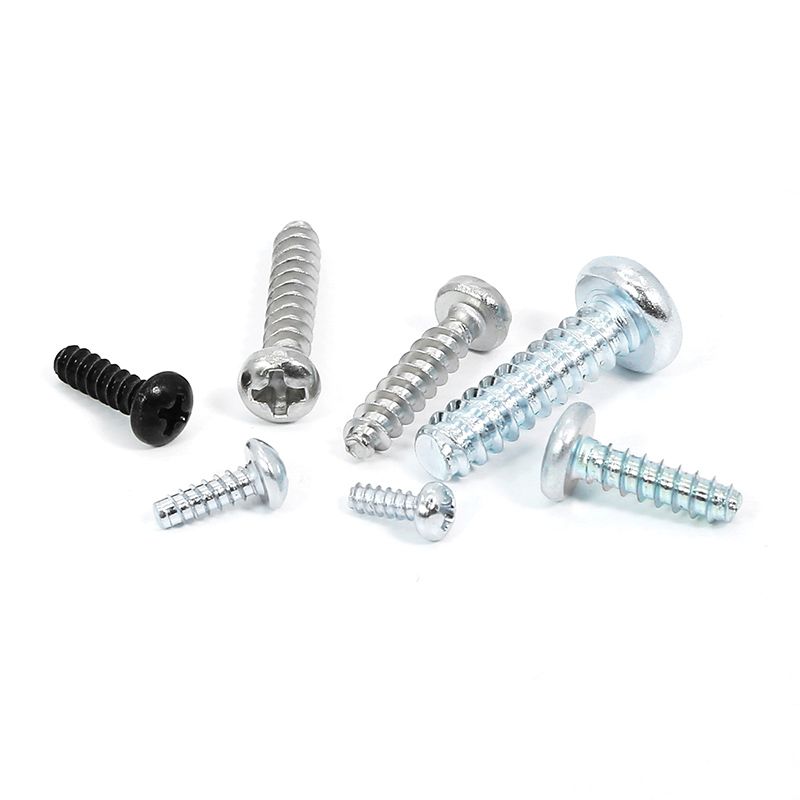
2. Фосфиране
Основен принцип е, че фосфирането е сравнително по -евтино от поцинковането, но устойчивостта на корозия е по -лоша от поцинковането. След фосфор, трябва да се прилага масло и нейната корозионна устойчивост е тясно свързана с работата на прилаганото масло. Например, след фосфиране, прилагането на общо масло от ръжда и провеждане на неутрален тест за спрей за сол само за 10-20 часа. Прилагането на висококачествено анти ръжда масло може да отнеме до 72-96 часа. Но цената му е 2-3 пъти по-голяма от тази на общото фосфатиращо масло.
Има два често използвани типа фосфатиране за крепежни елементи, фосфатиране на цинк и фосфация на базата на манган. Фосфирането на цинк на базата на цинк има по -добри характеристики на смазване от фосфата на базата на манган, а фосфирането на базата на манган има по -добра устойчивост на корозия и устойчивост на износване, отколкото цинковото покритие. Може да се използва при температури от 225 до 400 градуса по Фаренхайт (107-204 ℃). Особено за свързването на някои важни компоненти. Като свързващи болтове и гайки на двигателя, цилиндрова глава, основен лагер, болтове за маховик, болтове на колелата и гайки и др.
Болтовете с висока якост използват фосфатиране, което също може да избегне проблеми с водородното премахване. Следователно болтовете над 10.9 в индустриалното поле обикновено използват фосфативна повърхностна обработка.
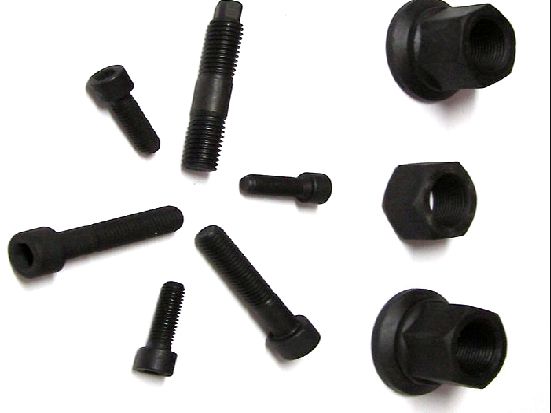
3. Окисляване (почерняване)
Изрязването+маслото е популярно покритие за промишлени крепежни елементи, защото е най -евтиното и изглежда добре преди разхода на гориво. Поради почерняването си, той почти няма способност за предотвратяване на ръжда, така че ще ръждясва бързо без масло. Дори в присъствието на масло тестът за спрей за сол може да продължи само 3-5 часа.
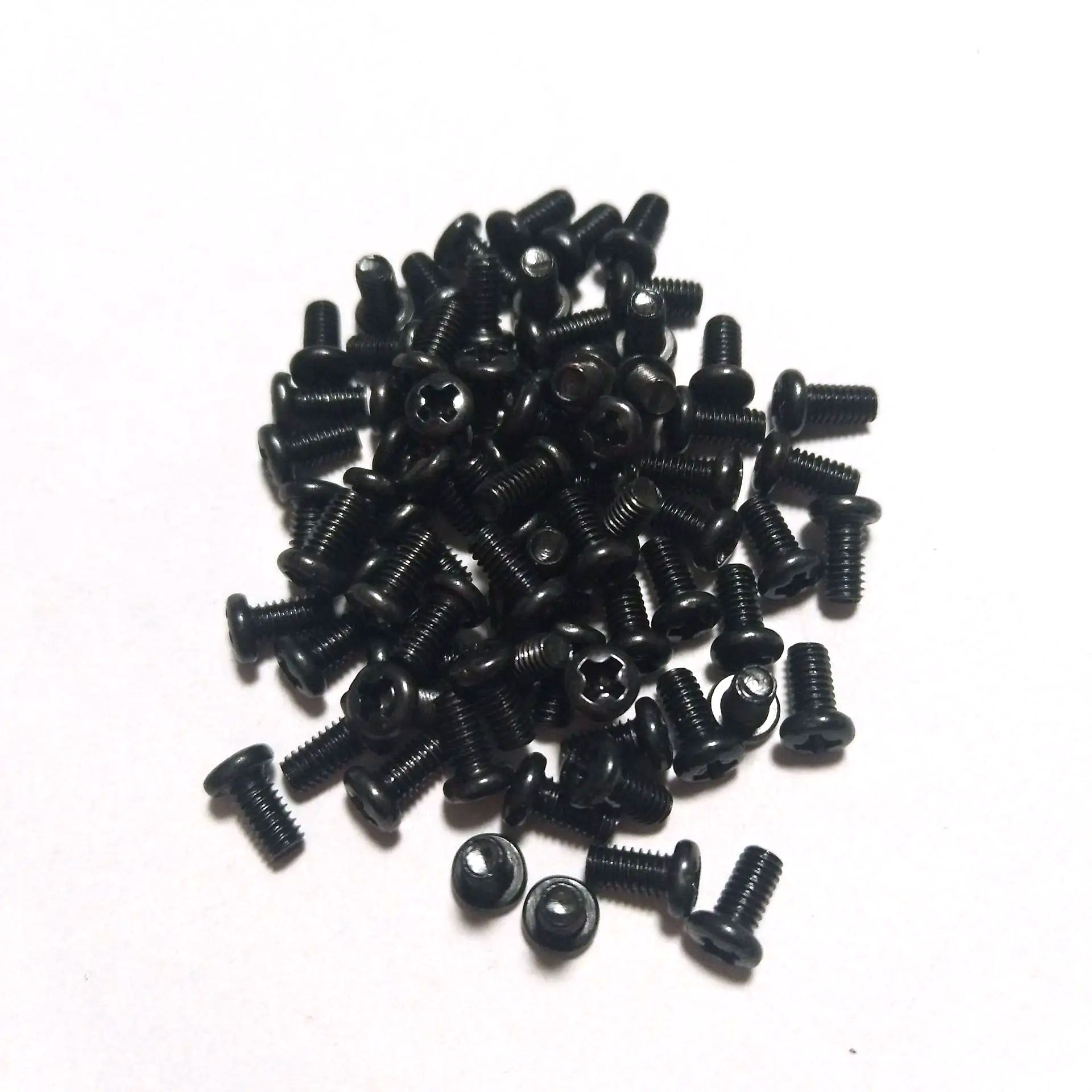
4. Разграждане на електроплаване
Кадмиевото покритие има отлична устойчивост на корозия, особено в морската атмосферна среда, в сравнение с други повърхностни обработки. Цената на пречистването на отпадъчните течности в процеса на електроплаване на кадмий е висока, а цената му е около 15-20 пъти по-голяма от тази на цинк за електроплаване. Така че той не се използва в общите индустрии, само за специфични среди. Закрепващи се, използвани за платформи за сондиране на нефт и HNA самолети.
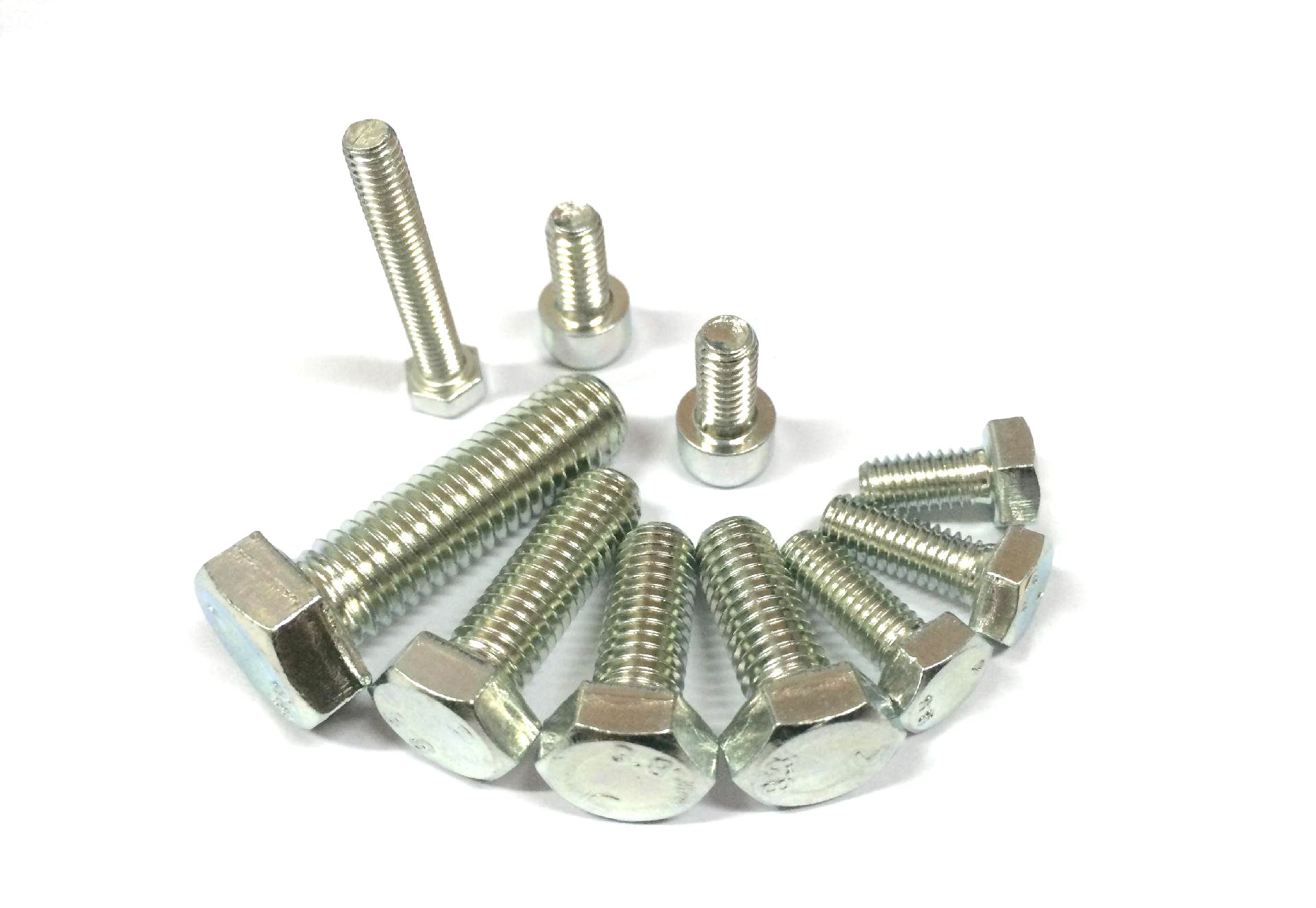
5. Хромово покритие
Хромното покритие е много стабилно в атмосферата, не е лесно да се промени цветът и да се губи блясък и има висока твърдост и добра устойчивост на износване. Използването на хромово покритие върху крепежни елементи обикновено се използва за декоративни цели. Рядко се използва в индустриални полета с високи изисквания за устойчивост на корозия, тъй като добрите хромирани крепежни елементи са еднакво скъпи, колкото и неръждаемата стомана. Само когато якостта от неръждаема стомана е недостатъчна, вместо това се използват хромирани крепежни елементи.
За да се предотврати корозията, първо трябва да се поставят медта и никел преди хромирането. Хромното покритие може да издържи високите температури от 1200 градуса по Фаренхайт (650 ℃). Но има и проблем с водородното премахване, подобен на електрогалванизирането.
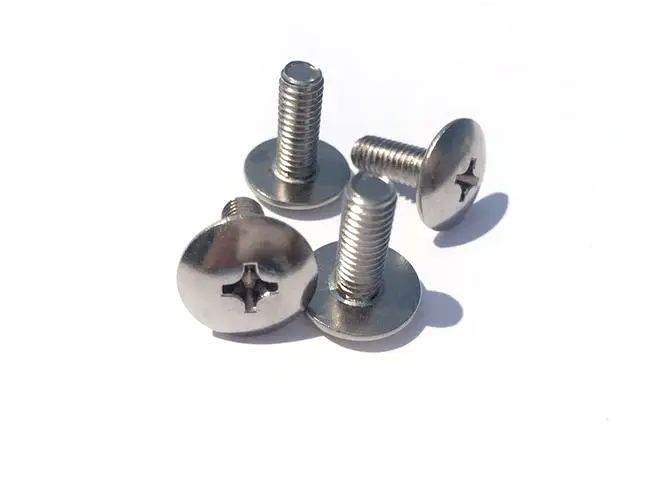
6. Никелово покритие
Използва се главно в области, които изискват както антикорозия, така и добра проводимост. Например изходящите терминали на батериите на превозното средство.
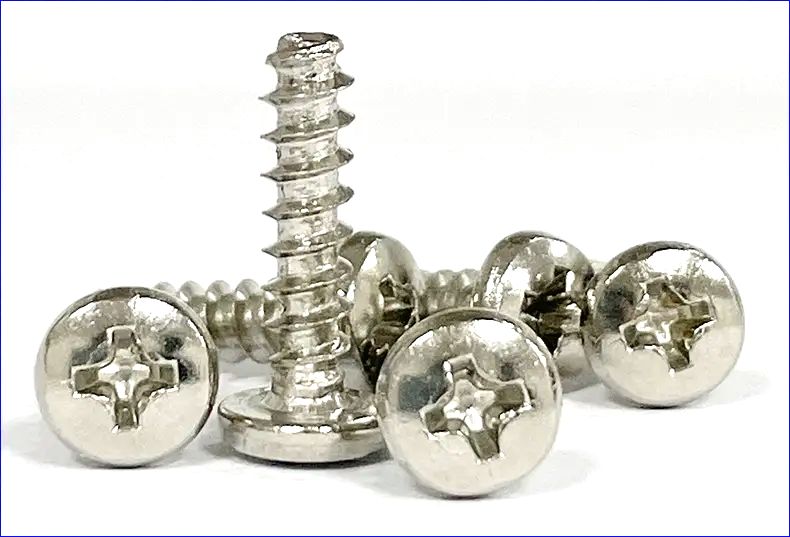
7. Главанизиране на горещо потапяне
Голванирането на горещо потапяне е термично дифузионно покритие на цинк, нагряващо се до течност. Дебелината на покритието е между 15 и 100 μm. И не е лесно да се контролира, но има добра устойчивост на корозия и често се използва в инженерството. По време на процеса на поцинковане на горещо потапяне има силно замърсяване, включително цинкови отпадъци и цинкови пари.
Поради гъстото покритие, то причини трудности при завинтване във вътрешни и външни нишки при крепежни елементи. Поради температурата на обработката на поцинковане с горещо намаляване, тя не може да се използва за крепежни елементи над 10,9 степен (340 ~ 500 ℃).
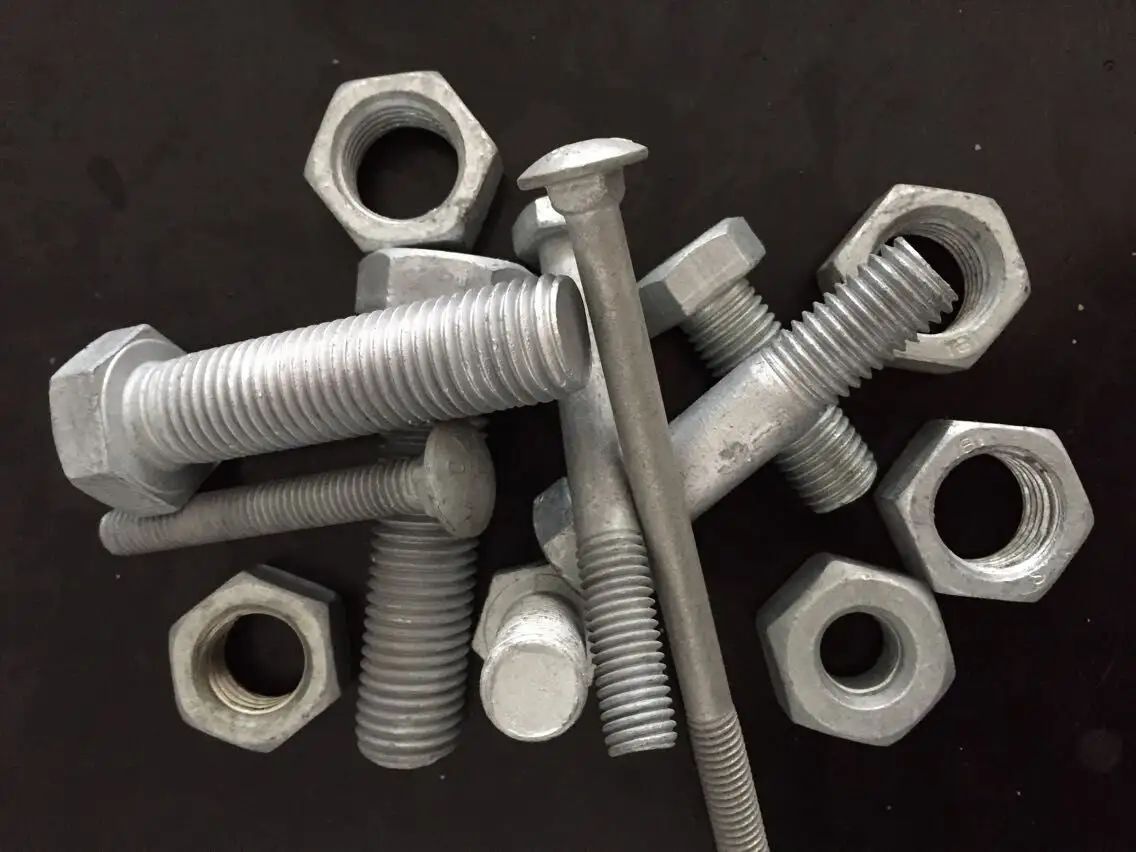
8. Цинк инфилтрация
Цинк инфилтрацията е твърдо металургично термично дифузионно покритие на цинков прах. Еднородността му е добра и може да се получи равномерен слой както в нишките, така и в слепите дупки. Дебелината на покритието е 10-110 μm. И грешката може да бъде контролирана при 10%. Неговата якост на свързване и ефективност на антикорозия със субстрата са най-добрите в цинковите покрития (като електрогалванизиране, галванизиране на горещо потапяне и дакромет). Процесът му на обработка е без замърсяване и е най-екологичният.
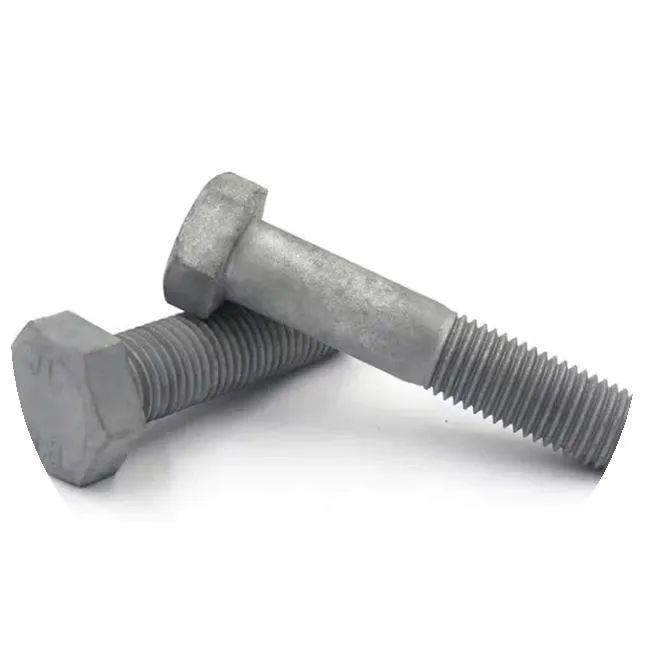
9. Dacromet
Няма проблем с водородното премахване и ефективността на консистенцията на напрежението е много добра. Без да обмисля хром и екологични проблеми, Dacromet всъщност е най-подходящият за крепежни елементи с висока якост с високи антикорозионни изисквания.
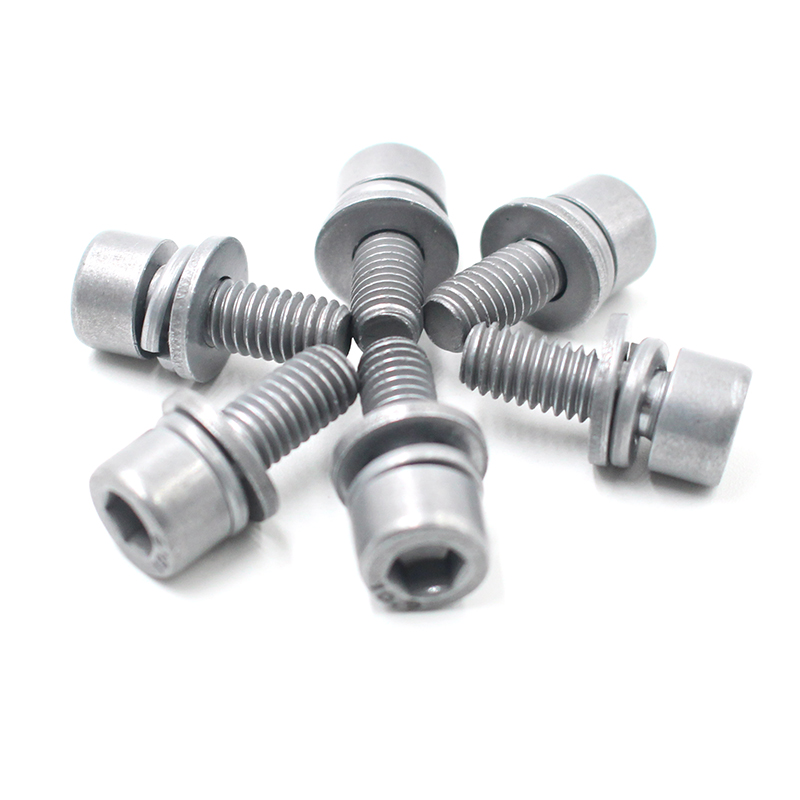
Време за публикация: май-19-2023